PVD coating (Physical Vapor Deposition coating) is a process used to deposit thin films of various materials onto a substrate using a vacuum process. The PVD coating process involves the deposition of a thin layer of a material onto a substrate in a vacuum chamber. The material is first vaporized using a high-energy source such as an electron beam, arc discharge, or sputtering source. The vaporized material then condenses on the surface of the substrate, forming a thin film.
PVD coatings are used for a variety of applications, including decorative coatings, wear-resistant coatings, and corrosion-resistant coatings. The process is commonly used to coat metal objects, such as watches, jewelry, and cutting tools, to improve their durability and appearance.
Another advantage of PVD coating is its versatility. The process can be used to deposit a wide range of materials, including metals, ceramics, and plastics. This allows for a variety of different coatings to be created with unique properties, such as wear resistance, corrosion resistance, and thermal stability.
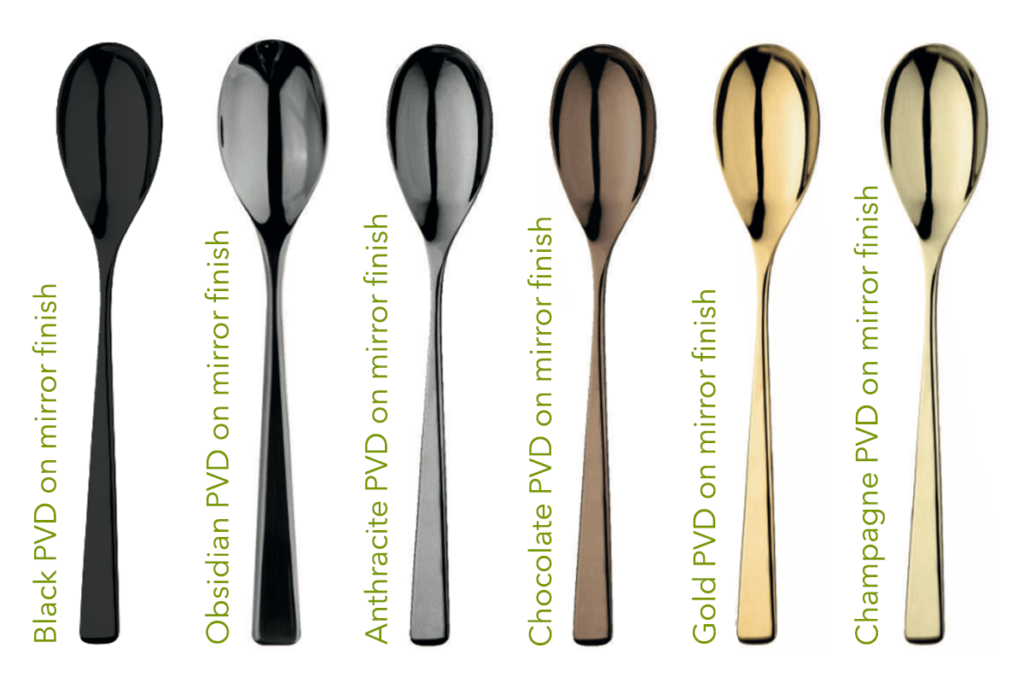
PVD coatings are used in a wide range of applications, including:
- Decorative Coatings: PVD coatings are often used to create decorative finishes on metal objects such as jewelry, watches, and other accessories. These coatings can create a wide range of colors and finishes, including gold, rose gold, silver, black, and more.
- Wear-Resistant Coatings: PVD coatings can be used to create wear-resistant coatings for tools, cutting blades, and other high-wear applications. These coatings can help to extend the life of these tools and reduce the need for frequent replacement.
- Corrosion-Resistant Coatings: PVD coatings can also be used to create corrosion-resistant coatings for metal components. These coatings can help to protect against corrosion and oxidation, which can extend the life of the component and improve its performance.
- Thermal Barrier Coatings: PVD coatings can be used to create thermal barrier coatings for high-temperature applications. These coatings can help to protect against heat damage and improve the performance of the component.
- Medical Implants: PVD coatings are also used in the medical industry to create coatings for implants such as joint replacements. These coatings can help to improve the biocompatibility of the implant and reduce the risk of rejection by the body.
The PVD coating process can be broken down into several steps:
- Cleaning and Preparation: The substrate must be cleaned and prepared before the coating process can begin. This typically involves removing any surface contaminants and roughening the surface to improve adhesion.
- Loading the Substrate: The substrate is then loaded into the vacuum chamber, where it will be coated.
- Deposition: The coating material is vaporized using a high-energy source and then deposited onto the substrate in the vacuum chamber. The thickness and composition of the coating can be controlled by adjusting the deposition parameters.
- Post-Deposition Treatment: After the coating is deposited, it may undergo post-deposition treatment to improve its properties. This can include annealing, which can improve the coating’s adhesion and hardness, or ion implantation, which can improve its wear resistance.
One of the key challenges in PVD coating is achieving good adhesion between the coating and the substrate. To address this, several techniques can be used, including ion etching to clean the substrate surface and improve adhesion, and the use of adhesion-promoting layers between the substrate and the coating.
In conclusion, PVD coating is a powerful technique for creating thin films with a wide range